White Crystal Stone, known for its beauty and luxury, is recognized as one of the most precious natural stones in both interior and exterior decor. This pure and uniform stone, with its brilliant white color and completely vein-free surface, evokes the image of fresh, dazzling snow at the height of winter. Just as snow transforms the surroundings into a calm and beautiful scene, White Crystal Stone also transforms your space with its unique qualities.
Using this stone in building facades, especially in high-end and exclusive projects, brings a sense of sophistication and modernity to the environment. Its light-reflecting ability creates a bright, inviting space that is not only beautiful but also imbues the area with positive energy and tranquility. When used for flooring, each step taken on White Crystal Stone provides a sense of softness and delicacy, transforming your home or workplace into a sanctuary of peace and beauty.
Due to its high durability and exceptional technical qualities, this stone is an ideal choice for unique places such as hotels, restaurants, and commercial spaces. By incorporating White Crystal Stone, you can bring life to a space that, with every glance, imparts a feeling of luxury and grandeur to guests and visitors alike.
Ultimately, White Crystal Stone is not only a symbol of beauty and luxury, but also a testament to your taste in choosing the finest for your living or work environment. Enter the exquisite world of this stone and bring the pure beauty of nature into your home. By selecting White Crystal Stone, you can add a modern, stylish look to your spaces, making each moment unforgettable.
Crystalline Marble
Premium White Chinese Marble.
Premium White Chinese Marble, composed of crystalline particles that allow light to pass through and offer high impact resistance, is an excellent choice for building facades in tropical regions
- ✅ high impact resistance
✅ very low water absorption.
✅ natural color.
✅ composed of crystalline particles.
✅ transmits light
✅suitable for engraving
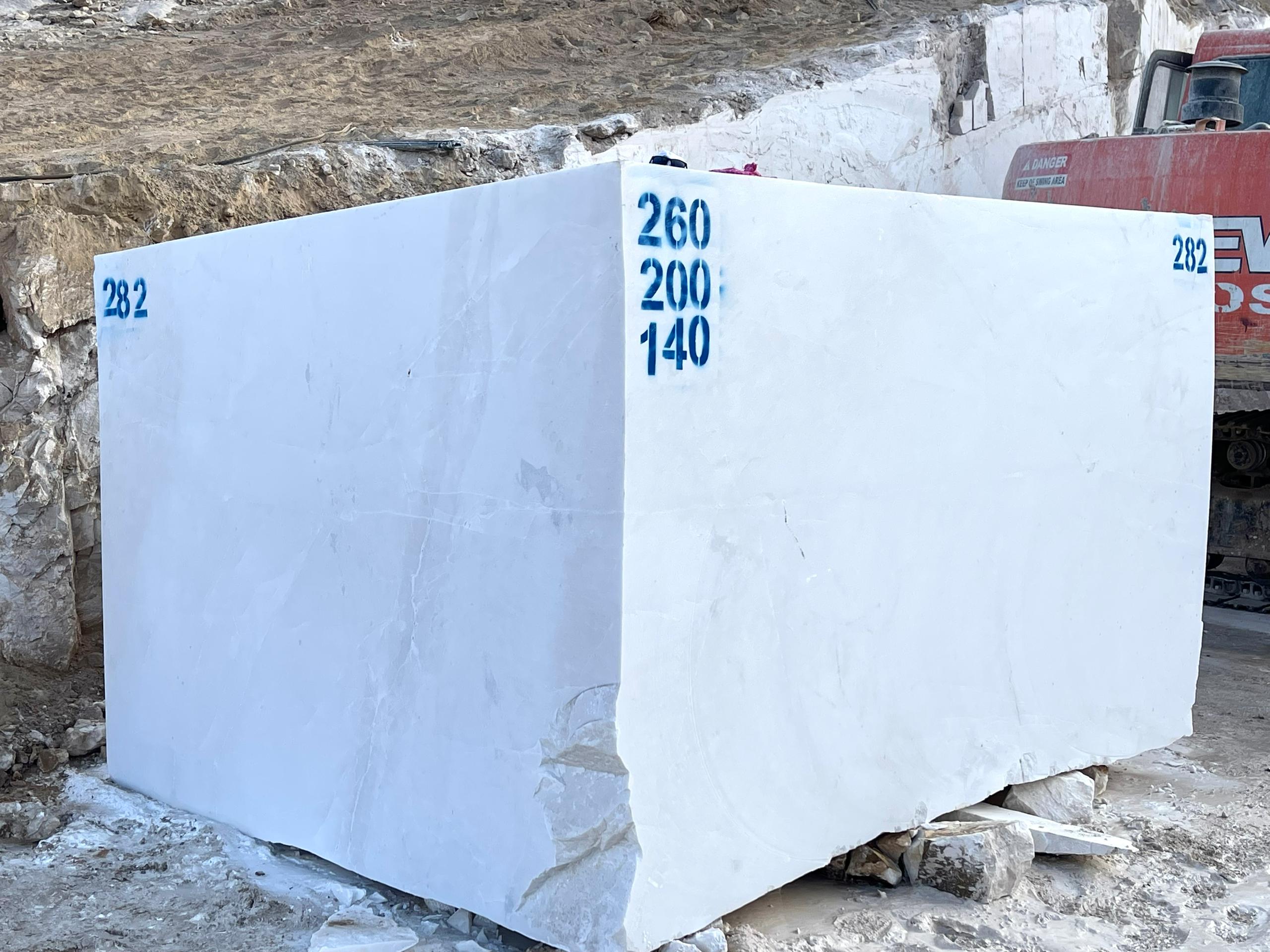
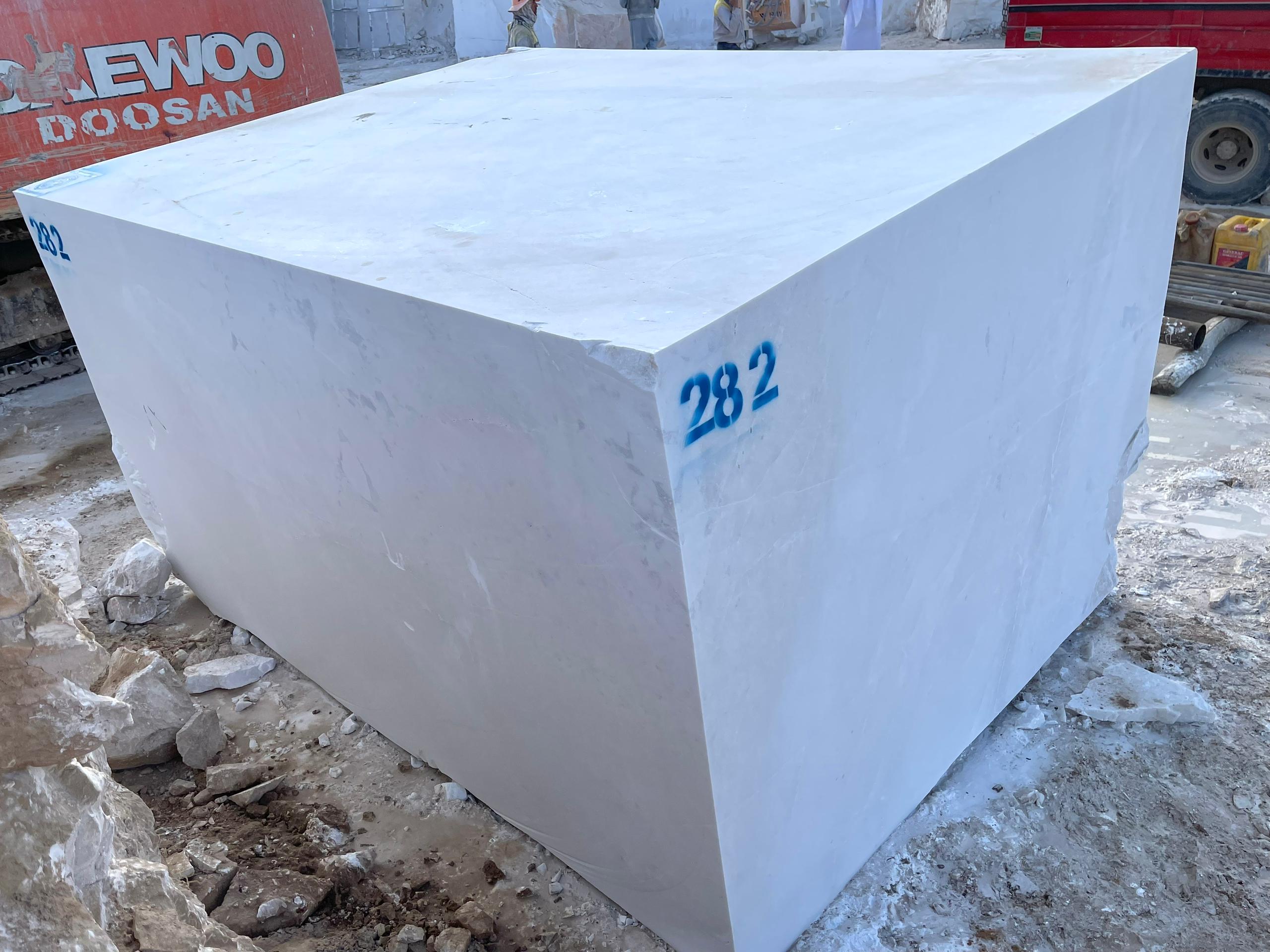
![1725954226943[1]](https://www.elysiumstone.com/wp-content/uploads/2024/10/17259542269431.jpg)
Crystalline Marble
White Crystalline Marble Grade2
Premium White Chinese Marble, composed of crystalline particles that allow light to pass through and offer high impact resistance, is an excellent choice for building facades in tropical regions
- ✅ high impact resistance
✅ very low water absorption.
✅ natural color.
✅ composed of crystalline particles.
✅ transmits light
✅suitable for engraving
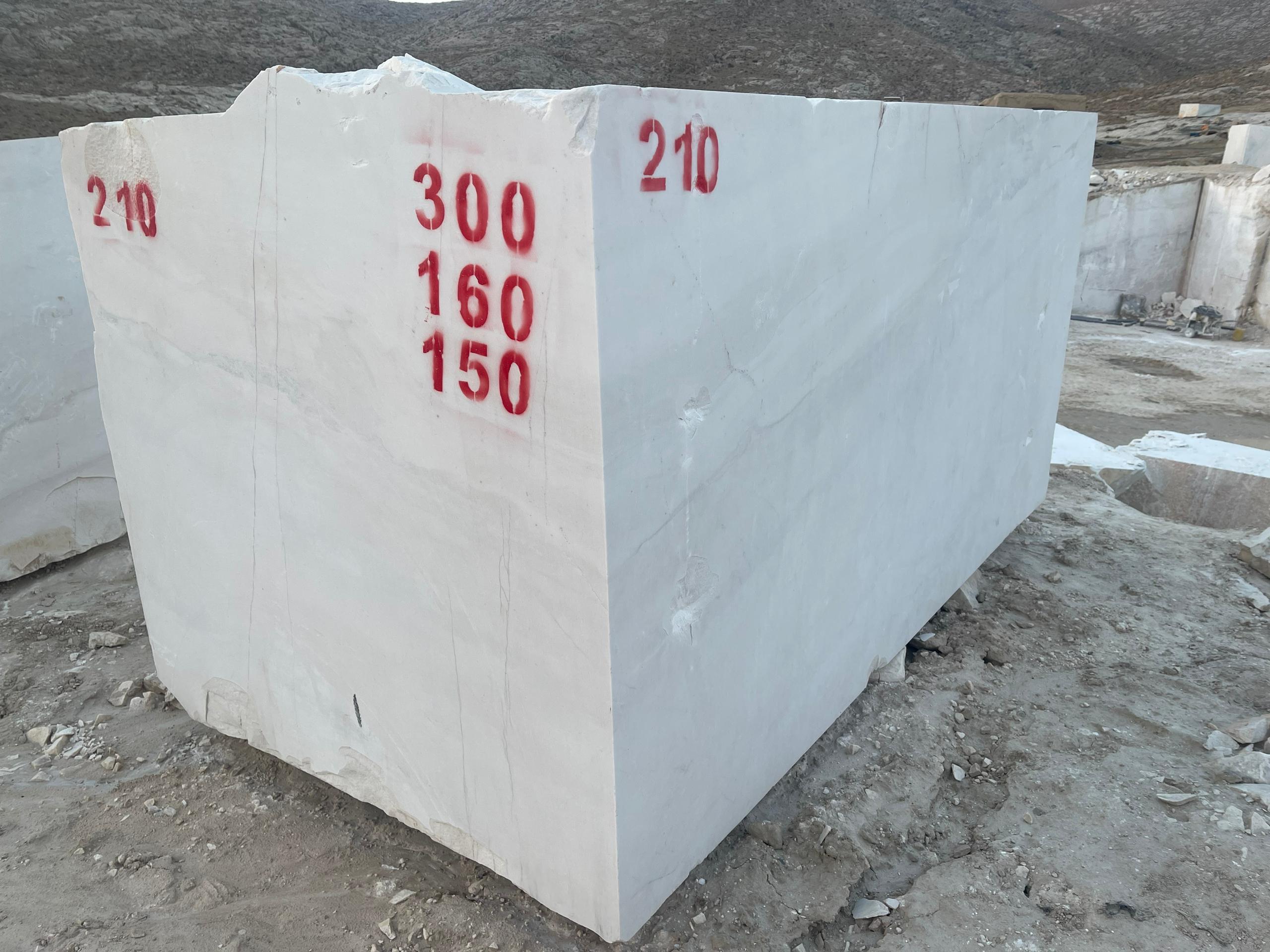
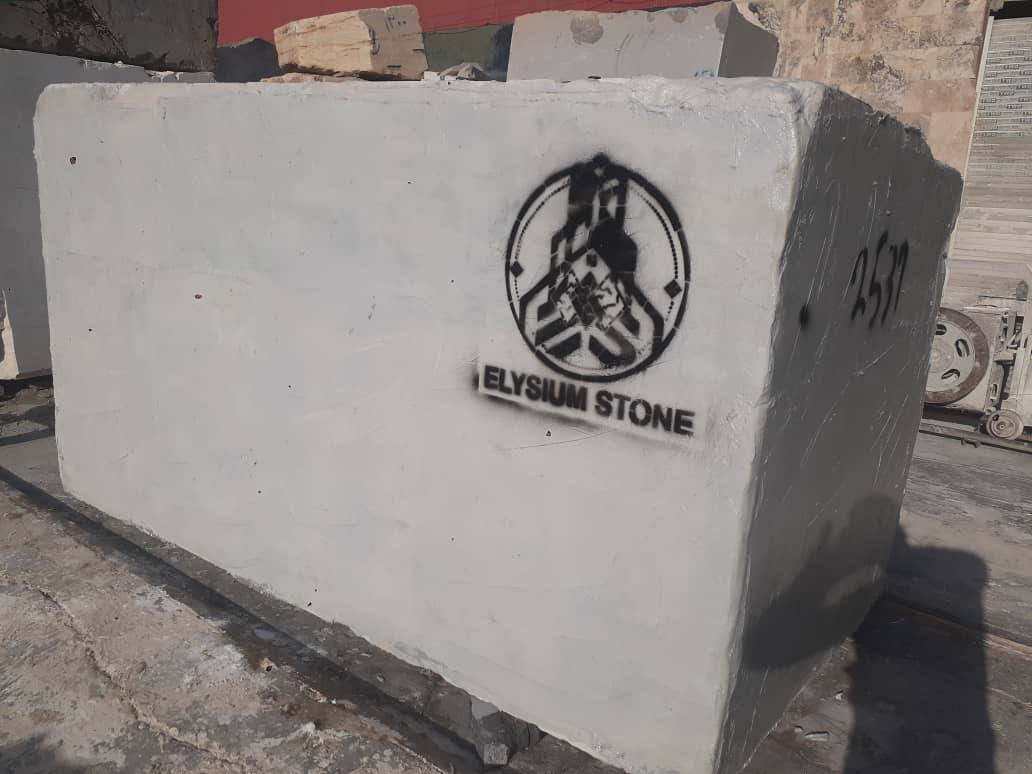
The process of slab production. White Crystalline Marble
Stage One: Block Bundle
1. Why Is Block Dressing Important?
Block dressing is one of the crucial stages in the stone cutting process for the following reasons:
Reduction of Internal Stresses: When stone is extracted from the quarry, internal stresses may arise. Block dressing helps to reduce these stresses, resulting in higher-quality stone.
Improvement of Surface Quality: This process ensures that the stone surface is smoother and more uniform, which is essential for subsequent cuts and slab production.
Minimization of Cracking Risk: By reducing internal stresses and improving surface quality, the likelihood of the stone cracking during later stages (such as cutting) is lessened.
2. How Is Block Dressing Done?
Use of Specialized Tools: In this stage, tools such as cutting blades, sanders, and specialized machines are employed to create a smooth and uniform surface.
Grinding Operations: The surface of the stone block is carefully ground to eliminate any defects or irregularities.
Testing and Quality Control: After block dressing, stones usually undergo quality control tests to ensure that stresses have been minimized and that the stone surface is suitable for cutting.
3. What Happens If Block Dressing Is Not Performed?
Increased Risk of Cracking: If the stones are not dressed, internal stresses may cause the stone to crack during cutting.
Reduced Quality of the Final Product: Unstable stones with uneven surfaces can lead to the production of low-quality slabs with an unattractive appearance.
Increased Costs: Producing low-quality slabs may result in higher repair or replacement costs, ultimately leading to decreased profitability.
Stage Two: Stone Cutting
Cutting stone blocks with a saw is a critical stage in the extraction and production of stone slabs. This process involves specialized cutting machines and encompasses several essential steps:
1. Selecting the Type of Saw
Disc Saw: This type of saw is typically used for straight and smooth cuts, making it suitable for cutting large and hard stones.
Chain Saw: Ideal for more precise and complex cuts, the chain saw offers greater flexibility in shaping and detailing stone.
Water-Cooled Saws: These saws utilize water as a coolant to manage temperature and prevent damage to the stone during the cutting process.
2. Preparing the Stone Block
Installation and Safety: Before cutting begins, the stone block must be carefully positioned at the cutting site. It should be secured to ensure stability and safety during the cutting process.
Machine Settings: The cutting depth and angle must be precisely adjusted based on the type and thickness of the stone to ensure optimal results.
3. The Cutting Process
Initiating the Cut: The saw machine starts cutting the stone block slowly and at a controlled speed. The operator must closely monitor the process to prevent any issues from arising.
Use of Cooling Fluids: Throughout the cutting operation, water or other cooling fluids are commonly used to reduce temperature and prevent cracking in the stone. These fluids also help lower friction and improve the quality of the cut.
Controlling Speed and Pressure: The cutting pressure and speed must be adjusted to maintain cutting quality and avoid damaging the stone. Excessive speed can lead to cracking and uneven cuts.
4. Quality Inspection of the Cut
Final Inspection: After cutting, the slabs are thoroughly examined to ensure there are no defects and that they meet quality standards. This inspection includes checking the surface, thickness, and uniformity of the slabs.
Quality Control Tests: Additional tests may be performed to assess the strength and quality of the slabs, ensuring they are fit for their intended applications.
Stage Three: Separation of Cut Slabs
The process of separating slabs is critical in stone production, ensuring that each piece is handled with care to maintain its quality. Below are the common methods used for separating slabs:
1. Using Hand Tools
In many cases, workers carefully separate slabs from one another using hand tools. This method requires a high level of precision to prevent damage to the edges and surface of the slabs. Skilled workers are essential in this process, as they can assess the slabs and handle them delicately to avoid chipping or cracking.
2. Separation Machines
In larger factories, automatic or semi-automatic machines may be employed for slab separation. These machines can efficiently and accurately separate slabs, significantly increasing productivity while minimizing human error. Their consistent performance ensures that slabs are handled uniformly, which is crucial for maintaining quality.
3. Stone Vacuums
For large and heavy slabs, stone vacuum devices are used. These machines utilize suction to lift slabs easily and without damaging their surfaces. The vacuum method allows for safe separation and movement, preventing scratches or other forms of damage that could occur during handling.
Stage Four: Mesh and Epoxy Resin
Applying Mesh and Epoxy to Slabs: Two Critical Stages in Finalizing Stone Products
The processes of applying mesh and epoxy to slabs are vital steps in finalizing stone products. These stages contribute to preserving the quality, strength, and aesthetic appeal of the slabs. Below, we will explain each of these steps, the reasons for their implementation, and the consequences of failing to execute them.
1. Applying Mesh to Slabs
Why is Mesh Applied?
Structural Reinforcement: Mesh is typically used to reinforce the structure of the slabs. Made from steel or other durable materials, these meshes help increase the strength and durability of the slabs, preventing them from cracking.
Preventing Warping: In cases where slabs are large and heavy, applying mesh helps prevent warping and damage during transportation or installation.
Impact Protection: Mesh can act as a protective layer, safeguarding against physical damage caused by impacts or sudden pressures.
What Happens if Mesh is Not Applied?
Increased Risk of Cracking: Failing to apply mesh to the slabs can result in cracking or breakage during transportation and installation.
Reduced Strength: Without mesh, the slabs may be more vulnerable to additional pressures and weights.
Shortened Lifespan: Slabs without mesh typically have a shorter lifespan and may require repairs or replacements sooner.
2. Applying Epoxy to Slabs
Why is Epoxy Applied?
Surface Enhancement: Epoxy is applied as a coating on the slab’s surface, providing a glossy and beautiful finish. This coating not only enhances the aesthetic appeal of the slabs but also protects their surfaces from environmental damage.
Moisture Prevention: Epoxy can prevent moisture from penetrating the stone, helping to avoid moisture-related damage.
Protection Against Stains and Contaminants: This layer acts as a barrier against stains and pollutants, making it easier to clean the slabs.
What Happens if Epoxy is Not Applied?
Environmental Damage: Not applying epoxy can lead to damage from moisture, pollution, and stains, which will affect the appearance and quality of the slabs over time.
Reduced Aesthetic Appeal: Slabs without epoxy may become dull and unattractive over time, losing their initial shine.
Increased Maintenance Needs: Without epoxy, slabs are likely to require more repairs and maintenance, which can be costly.
Stage Five: Drying the Slabs
The drying stage of slabs is one of the key steps in the production process of natural and artificial stones. This stage is carried out to reduce the moisture present in the slabs and prepare them for subsequent stages, including packaging and shipping. Below, we will explain the importance, process, and consequences of not performing this step.
1. Importance of Drying Slabs
Preventing Moisture Damage: Remaining moisture in the slabs can lead to severe damage such as cracking, swelling, and degradation of stone quality. Drying helps eliminate this moisture.
Enhancing Final Quality: Dried slabs generally have higher quality. This process helps maintain the beauty and structural integrity of the slabs.
Preventing Contamination: Moisture can promote the growth of microorganisms and fungi. Drying the slabs helps prevent these issues and extends the product’s lifespan.
2. The Drying Process of Slabs
Choosing a Drying Method: There are various methods for drying slabs, including natural methods (exposing to air) and artificial methods (using drying machines).
Drying at Suitable Temperature and Humidity: If drying machines are used, the temperature and humidity must be adjusted to gradually eliminate moisture without causing stress or damage to the surface of the slabs.
Drying Duration: The required drying time varies depending on the thickness and type of stone. Some stones may need more time to dry.
Quality Control: Throughout the drying process, the condition of the slabs should be continuously monitored to ensure that issues such as cracking or warping do not occur.
3. Consequences of Not Drying
Risk of Cracking: Inadequate drying can lead to cracking in the slabs, especially when they are subjected to varying temperature and humidity conditions.
Reduced Product Quality: Remaining moisture can lead to a decrease in the appearance and strength of the slabs, detracting from their beauty.
Increased Costs: Damaged slabs will require repair or replacement, which can lead to increased costs and ultimately reduce profitability.
Growth of Microorganisms: Moisture can cause the growth of fungi and bacteria, which can result in contamination and severe damage to the product.